
Reactor Sizing
1. Design the reactor that will be used in the proposed technology,
a.) What is the type of reactor to be used?
Continuous vertical plug flow is used.
Organic matter is constantly added or added in stages to the reactor. The end products are constantly or periodically removed, resulting in constant production of biogas. A single or multiple digesters in sequence may be used.
b.) Size of the reactor
c.) Operating temperature and pressure?
44-57°C. Thermophilic.
It has low energy consumption, produce low excess sludge production and more effective in energy recovery in
producing biogas.
d.)Does it require any heating/cooling? How do you provide that?
Digesters need to be kept at a steady, warm temperature for optimum gas yield and stable system operation. Ideally
digester heat requirements can be met by capturing waste heat from other facility unit operations, such as a
Combined Heat & Power (CHP) system. Sometimes, such as during start up, supplemental heat from a gas boiler is
required to get a system up to operating temperature. Heat can be applied internally to the tank through a series of
hot water pipes that are either embedded in concrete tank walls or supported on the inside tank walls. Heat can also
be applied externally to the tank from an external heat exchanger where contents from the tank are heated in either
a shell-in-tube or plate heat exchanger using a heat transfer fluid, usually water, that pulls heat from the CHP process
that has waste heat and moves heat to the tank contents.
e.) Cost of the reactor
(Refer to Coulson & Richardson Volume 6 or any chemical engineering design textbook to get the formula)
When a process or factory is designed, economy of the project needed to be taken into account. According to Coulson & Richardson Volume 6, these are some methods in cost estimation.
Method 1
The cost of equipment varies due to inflation. The change in equipment cost can be seen in statistical data and used for cost estimation in cost indexes. The indexes can be used estimation of cost for equipment of different sizes at different points in time. The following is the example of plant cost indices.
For example, In order to estimate the same plant cost in 2012, multiply the cost in 2009 with the ratio of the indexes
these years. Therefore, there are no corrections needed to be made as the cost of inflation has been taken account.
Method 2
To find the cost of plant built in 2013, statistical data for a few years before can be taken and an estimation is made based on a curve fitted to the data and extrapolate to 2013.
Method 3
If a newer plant with different size than the old one needed to be estimated, then formula below can estimate the cost of new plant at the same point as new plant.
Where
C2= Cost of plant with capacity S2
C1= Cost of plant with capacity S1
n=0.6
Method 4
If there is no old plant to compare with, factorial method can be used to estimate the cost of the whole plant from the cost of the major pieces of equipment.
The cost of individual parts of equipment can be estimated from historical data. The cost due to pressure rating and type of construction of the heat exchanger is taken into account using factors that are multiplied with the cost taken from the graph.

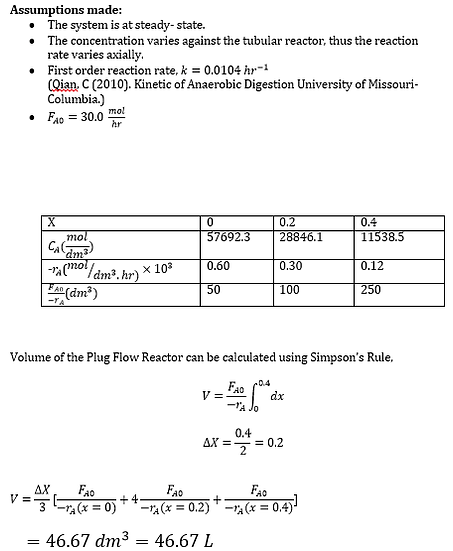
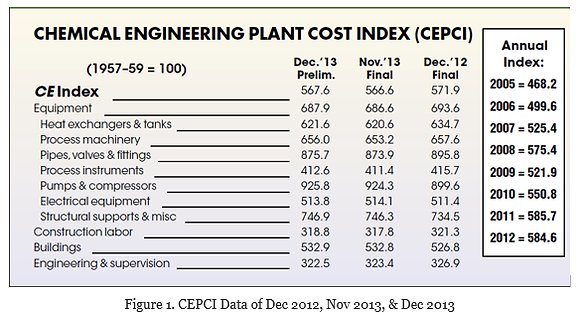


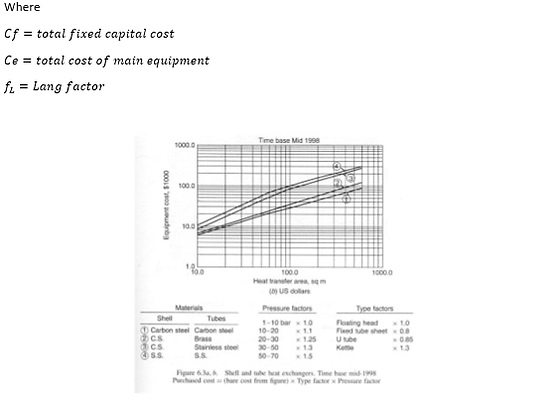
