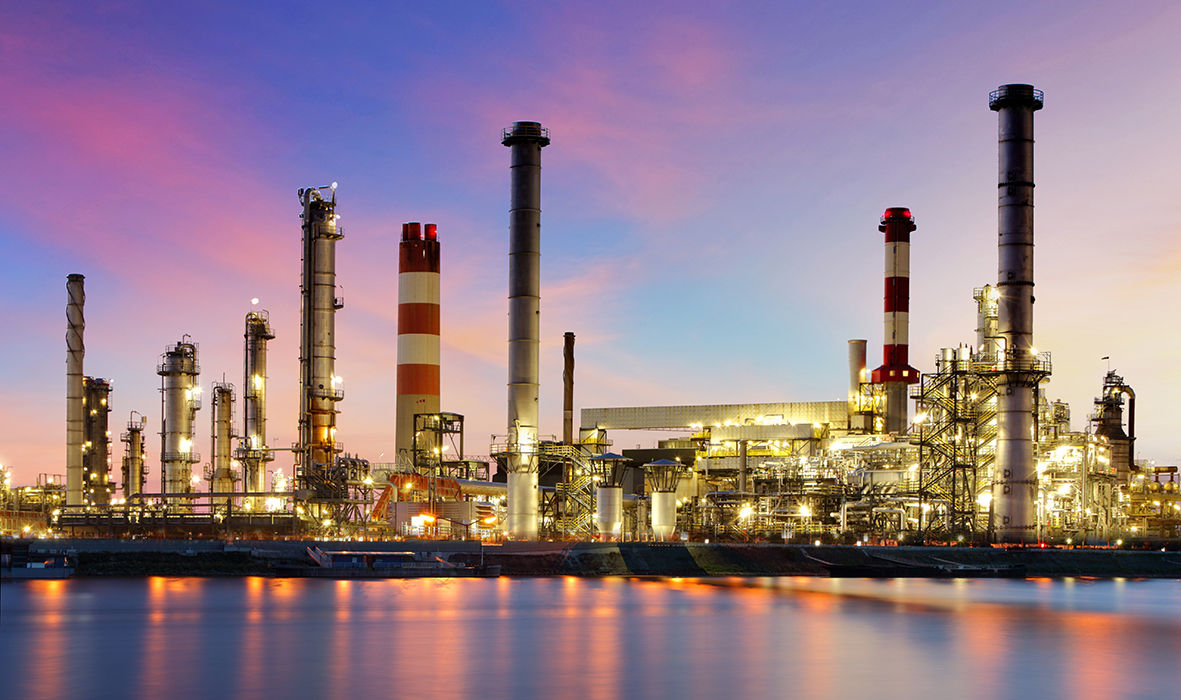
Literature Review
Energy is crucial for global prosperity, yet, fossil fuel reserves are depleting and becoming increasing inadequate to sustain the global energy demand. As such, the increasing use of fossil fuel, in parallel with increasing energy demand, has been the major cause for global warming and acid rain, which changes the earth’s environment, vegetation and ecosystem of aquatic beings (Dincer and Rosen, 1998). Global industrial plants currently produces more than a million tonnes of organic residue (wet weight) annually (Bolzonella et al., 2003). The recent hike in the energy cost, together with the increasing demand for energy, had increase the prospect of using alternative energy source. High organic content product contained in the vast quantity of effluents, as the result of industrial processes can be turned into continuous source of energy if managed correctly (Rajeshwari et al., 2000).
Anaerobic digestion
Anaerobic and aerobic reaction are occurring prevalently in nature. Anaerobic digestion is one of an effective ways to treat biological or organic waste, and turning it into a functional product that is of higher value. Anaerobic digestion had been in the spotlight since the early 1990s, where commercial and experimental anaerobic plant project was introduced (Karagiannidis and Perkoulidis, 2009). The generalised equation for organic decomposition by means of anaerobic degradation is as follows (Deublein and Steinhauser, 2008):
Anaerobic digestion is preferred over aerobic process as operation energy needed and biomass formed is lesser (Wang et al., 1999; Kim et al., 2006). The reaction also produces methane gas which is, a valuable product. As such, the following section will discuss on different technologies that uses anaerobic digestion as medium of reaction that turns waste into wealth currently used in different parts of the world.
Dry AD system
DRANCO technology is a patented improved version of conventional “wet” and “dry” digestion system. It is a proven and operational example of technology that uses anaerobic digestion (AD) principle as basis of operation in the facility. The biggest operational facility in Brecht, Belgium, have been operational for more than 10 years. It currently processes more than 50 kilo ton of waste annually. As a dry AD system, it operates at thermophilic temperature that is between 50 to 60 ⁰ C (De Baere, 2008). This temperature range helps to keep high level of hygienic since most of human pathogens are dead at these thermophilic range (Bendixen, 1994; Sahlstrom, 2003). Moreover, thermophilic operation enables higher rate of waste loading that can be processed and gives off higher concentration of methane than at mesophilic temperature range (Alastair et al., 2008).
Table 1 : Digestion result of plant using DRANCO technology
Dranco can process up to 50 % of overall solid concentrations which can be classified as “dry” (Mata-Alvarez, 2002). Dry AD have an advantage of requiring lesser volume, and consequently lesser number of digester compared to wet AD due to higher content of water exist in the sludge of wet AD. A single digester of 3150 m3 is able to digest 50 kilo tonne per annum of organic waste, producing 7.4 million m3 of biogas with 55% concentration of methane. These biogas yields about 10 million KWh of electricity per annum. According to Mashad et al. (2004), thermophilic condition is superior to mesophilic ones in the case of producing biogas by means of AD. This statement is further supported in the report by Fabien (2003), which explicitly states that operating at thermophilic condition, depending on the types of digester, can make the process become more efficient by having lower retention time, higher loading rate, and higher nominal gas production. The process was a continuous process, although it is not specified in the case study which continuous process it undergoes.
Table 2: Performance data of various anaerobic bioreactor for food and vegetable waste (FVW) treatment (Bouallagui et al., 2005)
Wet AD system
The term “wet” is a classification of the total solid percentage present in a waste sludge, which is typically lower than 16% (Alastair et al., 2008). Low solid materials such as food industry effluents and sewage sludge had been successfully treated and processed by this way. One such example or case study that depicts the usage of this wet AD system is thoroughly explained in a case study report of Ludlow (Greenfinch) Trial Scale Kitchen Waste Treatment Plant (Monson et al., 2007). The large scale pilot plant is located in Ludlow, United Kingdom, and has been running since March 2006. It collects 5000 tonne per annum of garden and kitchen waste from 19,000 households in the district of South Shropshire.
The plant itself operates at mesophilic temperature range (40⁰C), using a continuously stirred tank reactor (CSTR) as the anaerobic digester. There are some literature that suggests operating in mesophilic range is more stable and requires less energy expense (Ferna´ndez et al., 2007). However, Kim et al. (2006) found out that it is more efficient to produce biogas in the thermophilic range, rather than mesophilic range. The retention time for this system is 25 days (Monson et al., 2007). Since the plant operates as “wet” AD system, it requires a relatively higher tank volume compared to dry system due to presence of water in the sludge (Alastair et al., 2008). The scale of the plant inhibits profitability, due to the fact of higher cost per tonne of waste processed will be incurred for a larger plant.
Another case study by Monson et al. (2007) was conducted on different plant which was owned and operated by ZAK (Zweckverband Abfallbehandlung Kahlenberg) in Germany. Operating since 2006, this plant uses mechanical biological treatment (MBT) which includes mechanical and manual sorting, percolation and anaerobic digestion, biodrying, mechanical material separation and exhaust gas treatment. With wet AD retention time of 4 days, this plant treats about 100,000 tonne per annum of waste on comparatively small site (8000 – 9000 m2). The digester operates in parallel, but can be exclusively fed, controlled and supervised. The percentage of solid exists in the reactor is between 2.5 to 4%, and is operated in mesophilic range of 37⁰C.
Table 3 : Electricity balance from biogas produced on-site
The solid particles exists is separated between a few different fraction, and is percolated for 2 days, after which, it is then transported into biodrying hall, where it is aerated for 5 days which facilitates aerobic composting. The process is assumed to undergo the following generalized reaction, as it produces a considerable heat up to 55⁰C :
The heat reduces moisture percentage of waste which in turns decreases its mass and makes more suitable for use as a fuel. Exhaust gas is treated. The waste will now be categorised into solid recovered fuel/specific recovered fuel (SRF) and refuse-derived fuel (RDF) that can be sold off, attracting revenue for the plant operation. The drawback of this plant was that at the time of the case study, it is still new, as it was only into 6 weeks of running, so any teething or short term problem that arose as the result of new project were not known or revealed. The total cost of setting the plant at that time was £45 million pounds, and the cost per tonne of waste is £70.
REFERENCES
Alastair, J., Phil, J., Peter, J., & David, L. (2008). Optimisation of the anaerobic digestion of agricultural resources. Bioresource Technology, 99, 7928–7940-7928–7940. doi:10.1016/j.biortech.2008.02.044
Bendixen, H.J., 1994. Safeguards against pathogens in Danish biogas plants. WaterScience and Technology 30, 171–180.
Bolzonella, D., Battistoni, P., Mata-Alvarez, J., Cecchi, F., 2003. Anaerobic digestion of organic solid wastes: process behaviour in transient conditions. Water Sci. Technol. 48 (4), 1–8.
Bouallagui H., Ben Cheikh R., Marouani L., et Hamdi M. Fermentation méthanique des déchets solides en batch. Premières journées scientifiques de l’Association Tunisienne de Biotechnologie du 9–11 Février 2001.
Bouallagui,H., BenCheikh,R., Marouani,L., Hamdi,M., 2008. Mesophilic biogas production from fruit and vegetable waste in tubular digester. Bioresour Technol, 86 (2003), pp. 85–89
Bouallaguia,H., Touhamia,Y., Cheikh,R.B., Hamdia, M., 2005. Bioreactor performance in anaerobic digestion of fruit and vegetable wastes. Process Biochemistry, 40, 3-4, March 2005, 989-995. doi:10.1016/j.procbio.2004.03.007
De Baere, L.: The DRANCO process: a dry continuous digestion system for solid organic waste and energy crops. Presented at the IBBK Symposium on Anaerobic Dry Fermentation. 2008
Deublein, D. & Steinhauser, A., 2008. Biogas from Waste and Renewable Resources. Wiley-VCH, Weinheim
Dincer I., Rosen MA. A worldwide perspective on energy, environment and sustainable development. Int J Energy Res 1998;22:1350–61.
Fabian, M. (2003). An Introduction to Anaerobic Digestion of Organic Wastes. [online] Available at: http://www.biogasmax.co.uk/media/introanaerobicdigestion__073323000_1011_24042007.pdf [Accessed 26 Jul. 2015].
Ferna´ndez, J., Pe´rez, M., & Romero, L. (2008). Effect of substrate concentration on dry mesophilic anaerobic digestion of organic fraction of municipal solid waste (OFMSW). Bioresource Technology, 99, 6075-6080. doi:10.1016/j.biortech.2007.12.048
Kim, J.K., Oh, B.R., Chun, Y.N., Kim, S.W., 2006. Effects of temperature and hydraulic retention time on anaerobic digestion of food waste. J. Biosci. Bioeng. 102, 328–332.
Mashad, H.M., Zeeman, G., Loon, W.K.P., Bot, G.P.A., Lettinga, G., 2004. Effect of temperature and temperature fluctuation on thermophilic anaerobic digestion of cattle manure. Biores. Technol. 45 (2), 191–201.
Mata-Alvarez, J., Cecchi, F., Llabrés, P., Pavan, P., 1992 .Anaerobic digestion of the Barcelona central food market organic wastes: experimental study Bioresour Technol, 39 (1992), pp. 39–48
Mata-Alvarez, J., 2002. Biomethanization of the Organic Fraction of Municipal Solid Wastes. IWA Publishing.
Monson, K. D., Esteves, S. R., Guwy, A. J., Dinsdale, R. M. (2007). SOURCE SEGREGATED BIOWASTES. University of Glamorgan. Retrieved July 25, 2015 from http://www.walesadcentre.org.uk/Technologies/WetandDrySystems.aspx
Rajeshwari, K.V., Balakrishnan, M., Kansal,A., Lata, K., Kishore, V.V.N., 2000. State-of-the-art of anaerobic digestion technology for industrial wastewater treatment. Renewable and Sustainable Energy Reviews, 4, 135-156.
Rajeshwari, K.V. , Panth, D.C. , Lata, K. , Kishore, V.V.N., 1998. Studies on biomethanation of vegetable market waste Biogas Forum, 3 (1998), pp. 4–11
Rajeshwari, K.V., Panth, D.C., Lata, K., Kishore, V.V.N., 2001.Novel process using enhanced acidification and a UASB reactor for biomethanation of vegetable market waste Waste Manage Res, 1 (2001), pp. 292–300
Ruynal, J., Delgenes, J.P., Moletta, R., 1998.Tow phase anaerobic digestion of solid waste by a multiple liquefaction reactors process Bioresour Technol, 65 (1998), pp. 97–103
Sahlstrom, L., 2003. A review of survival of pathogenic bacteria in organic waste used in biogas plants. Bioresource Technology 87, 161–166.
Wang, Q., Kuninobu, M., Kakimoto, K., Ogawa, H.I., Kato, Y., 1999. Upgrading of anaerobic digestion of waste activated sludge by ultrasonic pretreatment. Bioresour. Technol. 68, 309–313.
Karagiannidis, A., Perkoulidis, G., 2009. A multi-criteria ranking of different technologies for the anaerobic digestion for energy recovery of the organic fraction of municipal solid wastes. Bioresour. Technol. 100, 2355–2360.
Verrier, D., Ray, F., Albagnac, G., 1987. Two-phase methanization of solid vegetable wastes Biol Wastes, 22 (1987), pp. 163–177


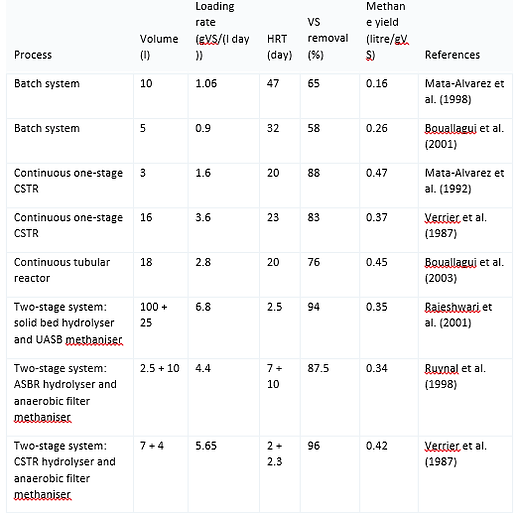

